Farason Corporation Application Spotlight: Mechanical Gripper with Custom Collar
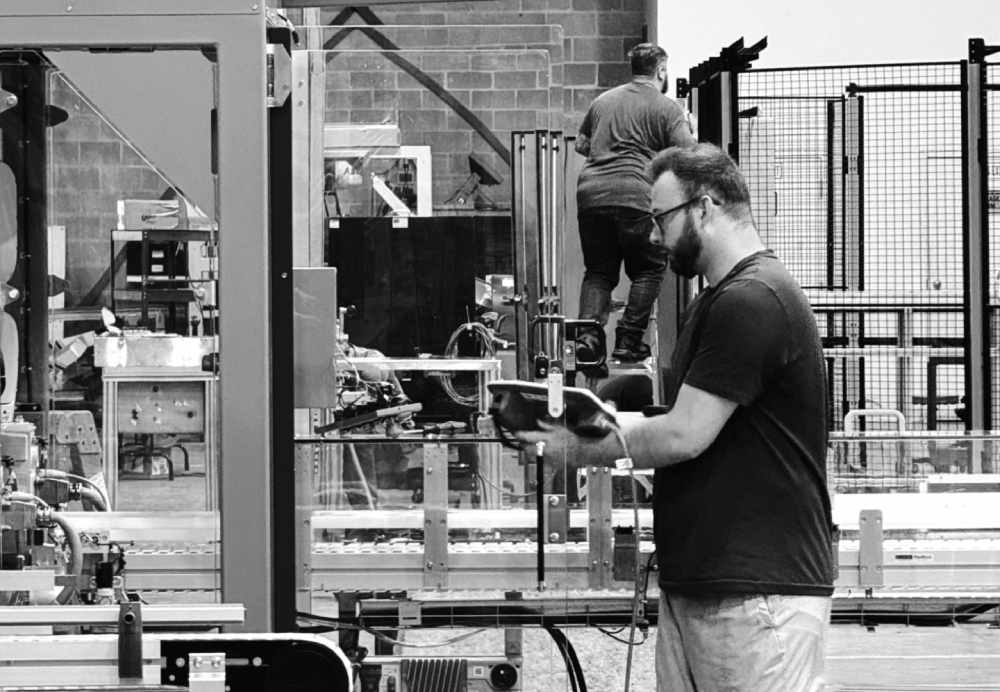
In this case study, Markforged highlights the innovative mechanical gripper developed by Farason Corporation. This gripper features a customized collar, enhancing its functionality and adaptability for various applications.
The Customer
For over thirty years, Farason Corporation has specialized in designing and delivering custom automation and robotics systems for manufacturers. They have successfully shipped over 900 machines to clients across North America, Asia, South America, and Europe. To enhance their design and production capabilities, the Farason team has integrated Markforged 3D printers into their offerings. This addition reflects Farason's commitment to providing unique solutions tailored to the specific challenges faced by their clients. Recently, the Farason Corporation team developed a mechanical gripper with a custom collar specifically for a robotics packaging automation application.
The Challenge
The automated design incorporates a robotic arm equipped with a two-way mechanical gripper specifically designed to grasp the neck of a plastic bucket. The gripper aligns with the threaded area to securely hold the bucket. Once it is grasped, the robotic arm lifts the bucket, swings it into position, and empties its contents into the next stage of product sorting.
The initial design of the gripper began with a 3D model of jaws that would lock around the neck of the target bucket, incorporating features to match the threading on the underside of the jaws. However, during testing, opportunities for enhancing its performance and effectiveness were identified.
The prototype was created to demonstrate the basic concept and successfully picked up the bucket, presenting it to the robot for dumping its contents. However, it was noted that a few bags were getting stuck between the mouth of the bucket and the funnel of the receiving receptacle.
The Solution
"We are able to iterate these quickly, adding this custom collar flange that helps contain the bags,” Design Support Engineer, Christian Weder said. “That would typically be an impossible feature.”He clarified that quickly fabricating the shape in a suitably light and durable material wasn’t feasible without the Markforged 3D printers, particularly for the low quantities required for creating such customized solutions.
Once the design was finalized, the team needed to prepare the production-ready final parts. Richard Cook, the designer and R&D Support Engineer at Farason, noted that while the proof-of-principle prototypes made from Onyx worked well for testing, relying solely on 3D printing with this material was not ideal. “They would be too rubbery,” Richard explained. “Given the cantilever design and the length of the part, you're essentially extending a substantial amount of material from a small pad with tiny bolts securing it to the gripper mechanism itself.”
To address this issue, the team incorporated Markforged’s continuous fiber reinforcement. Using Markforged X7 printers, they successfully produced the necessary parts to send to the customer. “We were able to use just a couple of layers of carbon fiber to demonstrate to the team that this material was the right choice,” Richard said. He emphasized the importance of ensuring support under the screws, adding washer plates to secure the assembly, and incorporating carbon fiber along the length of the finger to maintain stability and strength, preventing any twisting.
After printing a set of these parts, the team was very satisfied with the results. The finished end-of-arm tooling (EOAT) proved to be a success with the customer as well; it was durable enough to allow for slight bends, facilitating smooth movement and accurate positioning while remaining rigid enough to perform its intended function.
Markforged Printers Advantages
- Cheaper parts, delivered in hours not days
- Achieve complex features (the asymmetrical collar funnel) that could not be fabricated on-site affordably.
- 3D printing allows the team to optimize additively manufactured production solutions while testing.
- Continuous fiber reinforcement allows strength where it is needed while keeping the part light, rugged, and suited to the deployment.
“We can quickly iterate these by adding a custom collar flange that helps contain the bags, which would typically be an impossible feature.”
– Christian Weder, Design Support Engineer, Farason Corporation
The Conclusion
The integration of Markforged 3D printing technology at Farason Corporation has transformed their approach to custom automation and robotics solutions. By utilizing continuous fiber reinforcement and advanced additive manufacturing, they have been able to quickly and cost-effectively create lightweight, durable, and complex components. This innovation has not only enhanced the functionality of their robotic systems but also increased productivity, resulting in shorter lead times for their clients.
If a business wants to incorporate modern technology into its operations, Markforged 3D printing machines are a groundbreaking solution. Chemtron, one of the leading distributors in Asia, offers the services, technical support, and training necessary to facilitate a smooth transition to additive manufacturing. With Chemtron's guidance, you can fully harness the potential of 3D printing technology and enhance your business's efficiency and success.
Download the Free Report on How COVID-19 has Impacted Supply Chains
Gain key insights including: COVID-19 pandemic impact on business. 3D printing use during the health pandemic. Challenges facing manufacturers using incumbent technology. Future plans for investing in additive manufacturing. And more...
Get the report