Revolutionizing Industrial Automation: How McService Enhances Efficiency with the FX20™ 3D Printer
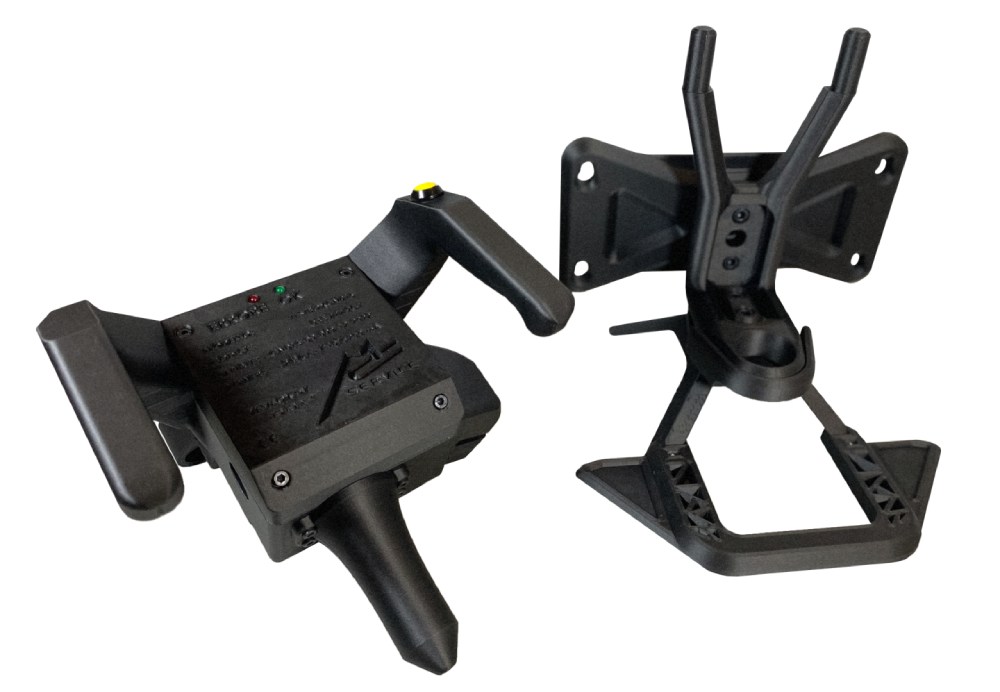
McService Overcomes the Limitations of Traditional Manufacturing with the FX20
Fixture for Verifying Gearbox Alignment
In the industrial machinery and equipment sector, customization and lead time are key drivers of competitiveness. McService, an Italian designer and manufacturer of industrial automation turnkey solutions, has successfully balanced these needs through the use of 3D printing.
The Challenge
Industrial production lines often need custom equipment to meet specific customer requirements. Traditional methods, like welding metal plates, can be time-consuming and costly, limiting their applications. This slows production, increases costs, and affects competitiveness. For example, creating a fixture to check the alignment of gearbox gears took significant time and used heavy materials like iron, negatively impacting tool ergonomics and prolonging production.
The Solution
To overcome these limitations, McService adopted Markforged industrial 3D printers, specifically the X7™ and FX20™, utilizing the composite material Onyx®. With these advanced technologies, the company has successfully produced customized parts while significantly reducing both time and costs.
The gear alignment verification fixture, manufactured on the FX20, includes an electronic board for audio and visual feedback, along with built-in handles for added comfort. Custom labels with instructions and logos are easily printed using the Digital Forge™ platform, which enhances the product's features.
Benefits
The use of 3D printing has yielded many tangible advantages:
- Large and high-strength part production: With the FX20, McService can produce robust and functional parts with large dimensions, perfectly suited for advanced industrial applications.
- Time savings: Using traditional methods, the production of the gear alignment verification fixture took about two weeks. With the FX20's print speed, the piece can be printed in just 1.5 days.
- Cost savings: The use of Onyx material instead of welding processes has resulted in a 40% cost savings for the fixture.
- Weight savings: The 3D-printed fixture weighs 1 kg, significantly lighter than the conventional iron version, which weighs 2.5 kg. This weight reduction has made the tool more ergonomic for operators.
- Design flexibility: The design freedom of 3D printing has enabled the inclusion of innovative functionalities and customizations without extra cost.
Using Markforged's FX20 printer and Onyx material, McService streamlined a complex process into a quick, efficient, and ergonomic solution, establishing itself as a leader in implementing innovative technologies for industrial automation.
The Conclusion
For organizations seeking to integrate advanced technology, the implementation of Markforged 3D printing machines by McService exemplifies the transformative potential of additive manufacturing. These innovative solutions enhance production efficiency and minimize lead times. With the support of Chemtron, a prominent distributor in Asia, businesses can access vital tools, comprehensive training, and technical expertise necessary for a seamless transition. By capitalizing on Chemtron's insights and the capabilities of Markforged, organizations can realize significant advancements in both productivity and sustainability.
Download the Free Report on How COVID-19 has Impacted Supply Chains
Gain key insights including: COVID-19 pandemic impact on business. 3D printing use during the health pandemic. Challenges facing manufacturers using incumbent technology. Future plans for investing in additive manufacturing. And more...
Get the eport